Introduction
Wear and tear are the main reasons for maintenance and unexpected and often costly shutdowns of plants in the cement, chemical, steel and mining industry. The use of very abrasive materials like cement, coal and minerals which are transported with high velocities and handled in often huge amounts per hour using hydraulic and pneumatic transport systems in for example linings, chutes and silos is resulting in a continuous erosion of transport and storage equipment. An unplanned shutdown to repair or replace a worn-out bend used to transport pulverized coal to the boiler of a powerplant is not only very expensive but can also result in problems with power supply services to consumer and industry.
Applications
Ultra High Performance Concrete (UHPC) as wear lining has a very long track record of > 40 years. Prefabricated bolt on wear panels, pipe and bends with an UHPC lining and shotcreted or hand patched linings are designed and produced daily. The possibility to vary the thickness of the UHPC wear lining in locations with potential heavy wear gives extra flexibility in the design and extends the service life.
But these wear protection experiences can also be used in other applications where heavy daily wear and tear is unavoidable like for example cavitation erosion in dams, sluices and waterways and industrial floors, pavements and other structures exposed to extreme heavy wear. The ASTM C 1138-97 test, developed by U. S. Army Engineer Waterways Experiment Station (WES), Vicksburg, MS. To simulate extreme cavitation erosion, like in hydraulic structures, showed large abrasion-erosion from the steel grinding balls but no noticeable wear of the UHPC in Edelca’s laboratory (Venezuela) in 1992. One of the first large wear related applications was the rehabilitation of the Kinzua Dam Stilling Basin in October and November 1983. This basin had, despite earlier repairs in 1973 – 1974, also due to cavitation erosion, worn-out concrete up to 1.10 m1 depth in the 1.50 m1 thick concrete slab. The specified unreinforced 1.540 m3 UHPC with a thickness of 30 cm and with a compressive strength of >90 Mpa was placed in sections. Despite several problems, most of them related to the lack of sufficient knowledge and experience with UHPC, like sensitivity for plastic shrinkage cracks, autogenous shrinkage, applicability, and workability, the overlay is working according to the expectations. With the present knowledge it would be better to place a steel fiber reinforced HPC concrete as levelling layer with a bonded fiber reinforced high wear resistant overlay of 5 cm UHPC with calcined bauxite aggregates.
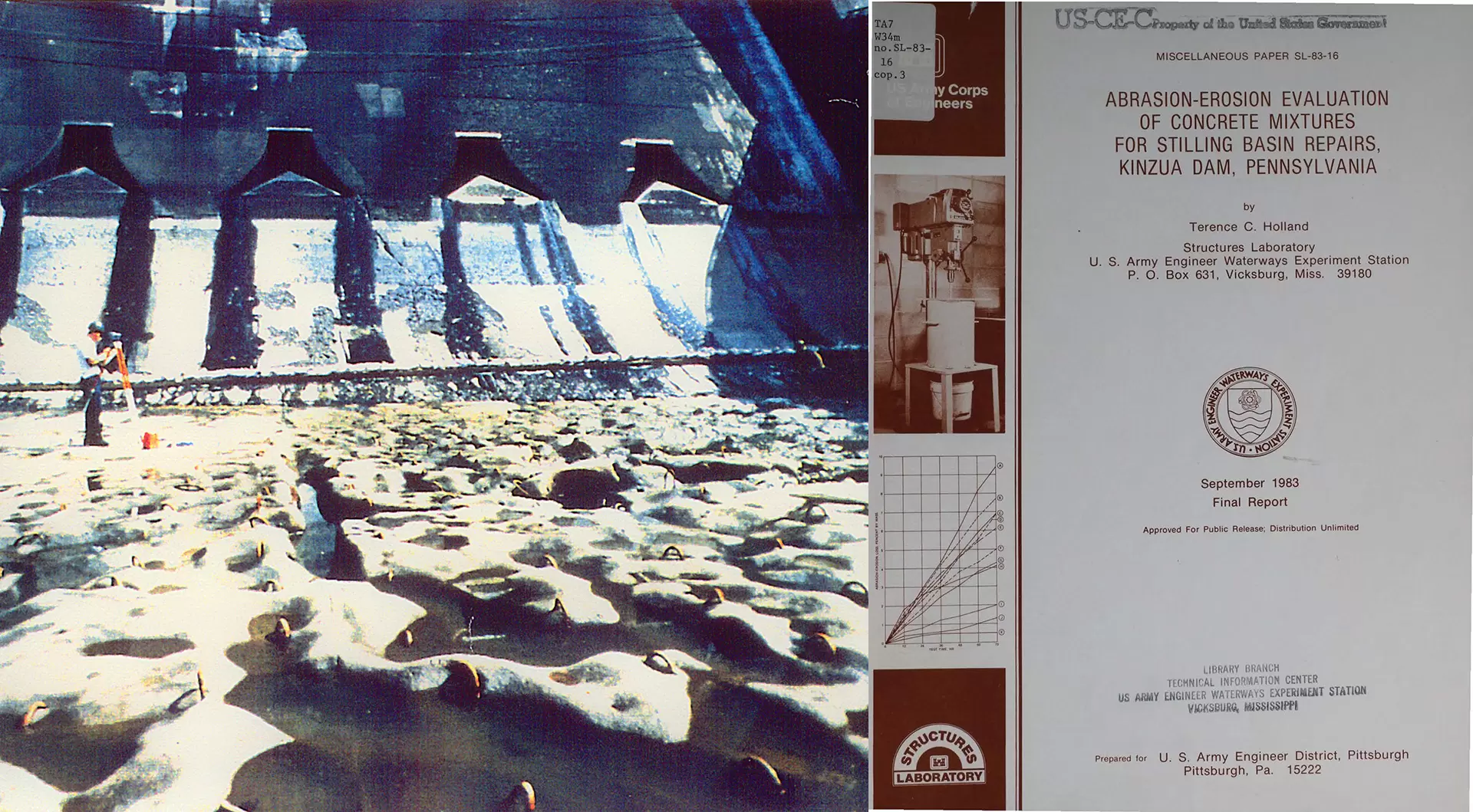
Extreme wear of concrete in stilling basin Kinzua dam which was rehabilitated with a layer of UHPC.
Because of the connection with Aalborg Portland, and thus also being member of the FLS Group, the world’s first supplier of UHPC had the possibility to use the newly developed materials (1978) as wear protection in hydraulic- and pneumatic transport systems and storage systems in Aalborg Portland’s own cement factory and many other cement factories around the globe. The UHPC has been used also for the replacement of cast steel and cast-iron machine parts.
A good example is the replacement of the cast-iron scoop feeders for a cement mill with replaceable sections cast in hybrid reinforced UHPC with a much longer service life, 15 – 20 years instead of 6 months, compared to the original cast-iron scoop feeder. During his practical training in 1986 the author had to cast several bends and panels and trowel a lining of a scoop feeder housing.

Application of UHPC wear lining inside house of scoop feeder cement plant and casting UHPC scoop feeder section.
However, there are no “all problem” solving materials for wear protection. Abrasion or wearing is a very complex process and sometimes a cheap rubber lining will perform much better than an expensive ceramic wear lining. The total service life of the wear protection lining depends on the properties of the product responsible for the wear: particle size, - hardness, - angularity, and humidity, angle of contact, velocity, and temperature.
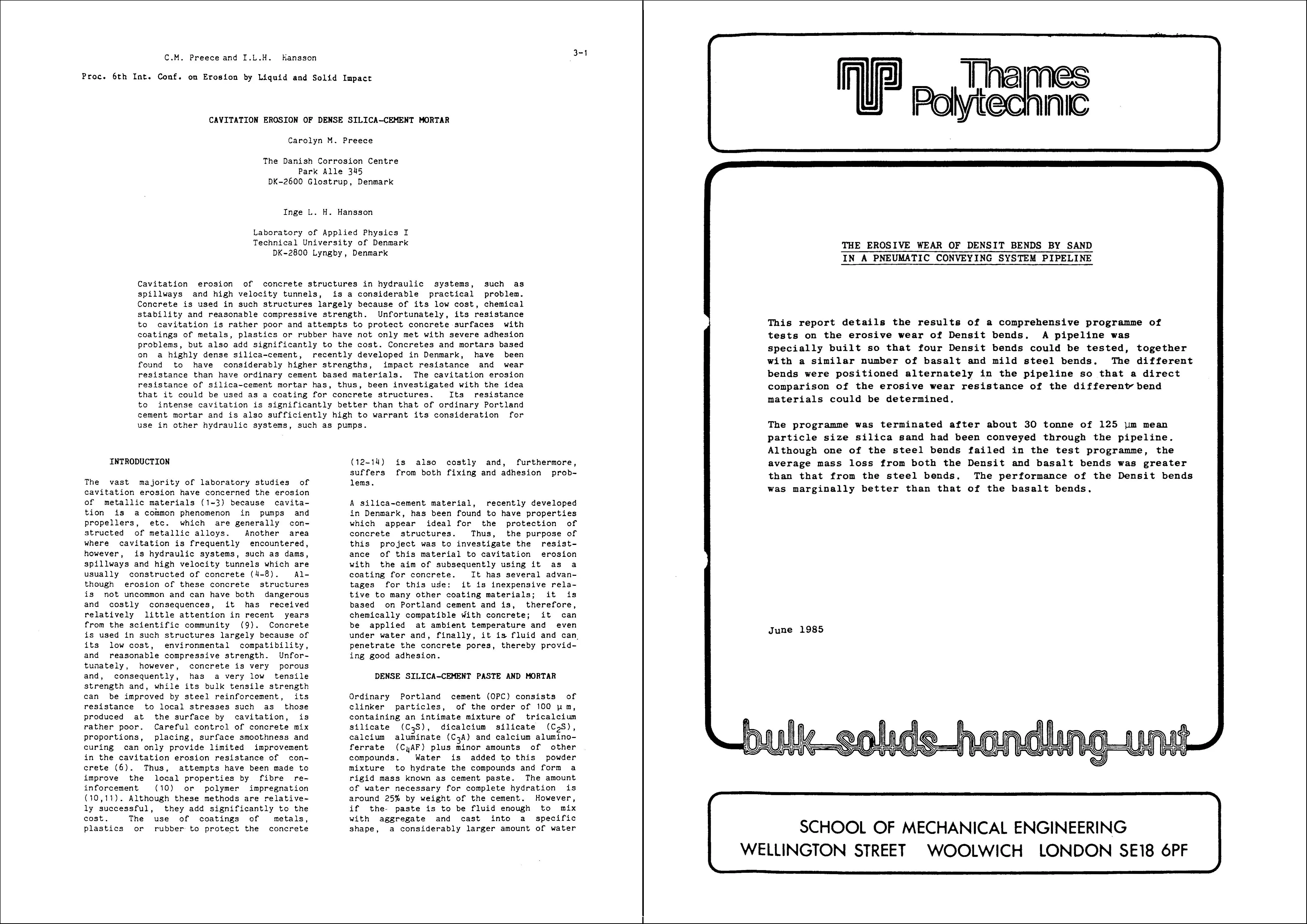
Paper Carolyn M. Preece and Inge L.H. Hansson 1983 regarding cavitation erosion UHPC and wear Performance test of bends with a lining of UHPC and with a lining of castbasalt in comparison with steel bends at Thames Polytechnic 1985.
Since the development in 1978 (Hans Henrik Bache Aalborg Portland) UHPC has been tested, investigated, and used for wear protection in industry and for structures.
The specific UHPC is combining the binder with very hard high-quality aggregates like quartz, calcined bauxite, corundum and silicon carbide and steel fibers. A special binder with selected aggregates and stainless-steel fibers is used for temperatures in the range of > 400 – 1200 °C.
The UHPC has the following advantages in wear protection:
• Application: casting, shotcrete, hand patch.
• Application of a new layer and/or repair with a new layer is possible.
• Wear resistance: equal to that of melted basalt, special steel and high-tech ceramic materials.
• Wear resistance and impact resistance can be designed with the use of selected aggregates and fibers.
• To cast in-situ and jointless or prefab.
• Impact resistance: high – very high, especially compared to wear resistance tiles.
• Temperature range: - 50°C - +1200 °C (special binder and selected aggregates and fibers).
Compressive strength or Performance?
For wear linings and other wear related applications of UHPC the compressive strength is not the most important performance; wear -, impact- and heat resistance are much more important. There is also no direct relation between compressive strength and wear resistance of UHPC. The hardness, impact strength, diameter and wear resistance of the aggregates used are much more important. The controlled autogenous shrinkage is in this case contributing to the wear resistance of the UHPC because it is enhancing the interface aggregate and binder and holding the wear resistant aggregate and fibers in a very strong “embrace” to secure that wear resistant aggregates are wearing or resisting wear instead of being removed partly or even completely by impact and abrasion. This is often the case in traditional concrete where the binder phase is deteriorating fast and too weak and porous to secure a good and durable bonding on hard aggregates. Compare it to a diamond in a ring, the diamond is extremely wear resistant and hard but when the head or setting is not placed correctly the grip on the precious stone will be weak and the diamond will be easily removed out of its mount despite its hardness and wear resistance. A certain shrinkage is thus positive in this case and “increasing the grip strength” on the wear resistant aggregates.
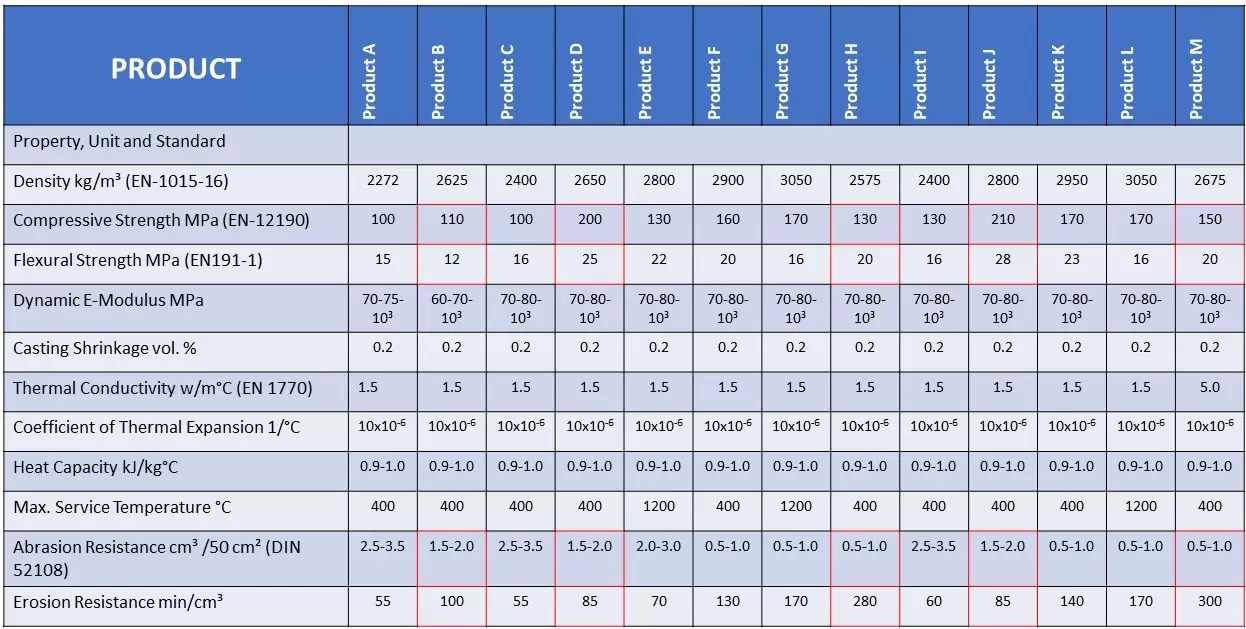
Range of standard UHPC products for wear protection and their properties.
My thoughts about UHPC for wear protection: Performance is the key factor!
We learned from the different wear tests and methods (Böhme abrasion test, Densit abrasion test, ASTM C 1138-97 abrasion test and different tests for flooring materials) and thousands of practical applications that there is a market segment where UHPC is performing excellent for wear protection and an interesting alternative for concrete and other materials. The experiences during the last decades should be used to obtain knowledge regarding UHPC and its performance under heavy wear and the composition possibilities of UHPC to obtain the performance needed for a certain project taking total costs and resources efficiency in account.
Share on