Special surfaces have always been possible with GRC. Whether due to a market trend or improvement of production techniques, more and more projects are emerging with special surfaces, and architects increasingly ask for a wider variety of options.
In broad terms, there are two options for creating specialised surfaces: precasting and post-casting. Precasting is the skill of creating a mould that forms the invert of the desired surface, whereas post-casting is a process conducted on the element after demoulding.
Combining the 3D capability of sprayed GRC with exposing the aggregate is popular for both renovation projects and new buildings. The exposed aggregate creates a less uniform surface and adds texture to elements. Typically, four different techniques are used to expose the aggregate: grinding, sandblasting, retarder paper and washing. Previously, acid etching was also frequently used; however, this is now in steady decline.
The post-casting techniques are simply just different ways of exposing the aggregate. It is a matter of best technique for the required look of the elements. It is a question of roughness/smoothness of the surface and the amount of aggregate to be visible.
Retarder paper is a little different from the other techniques and is, as the name implies, always dependent on the retarder in the paper. The retarder paper can give very fine patterns or images by removing the cement’s ‘skin’ in selected areas. It is even possible to have photos made into a retarder paper and have these forever imprinted in concrete.
For renovation projects it is a question of mimicking the previous concrete façade, while replacing it with a much thinner and more durable version that allows room for extra insulation, etc. There can even be preservation reasons for having the GRC to precisely match the previous surface.
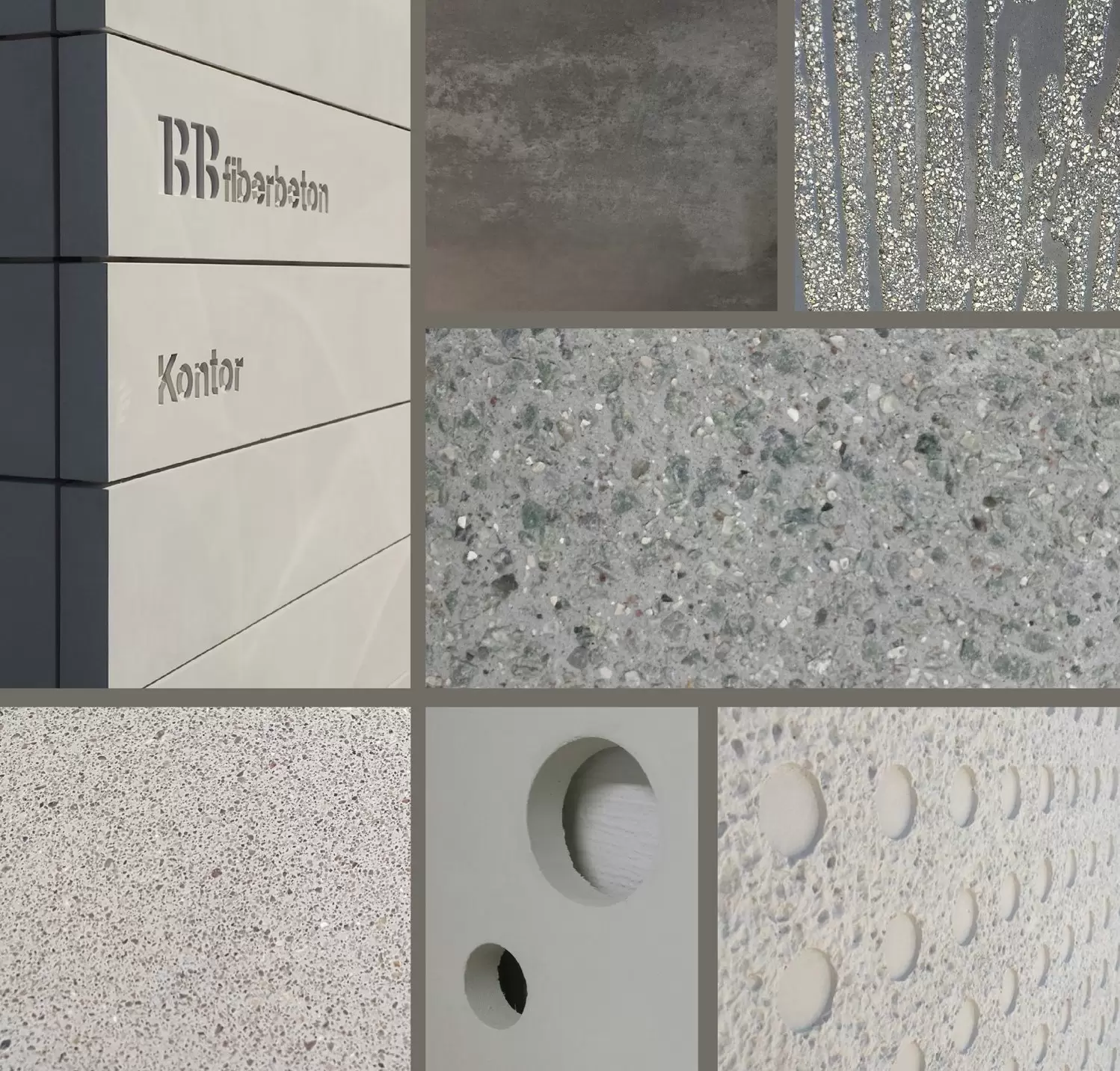
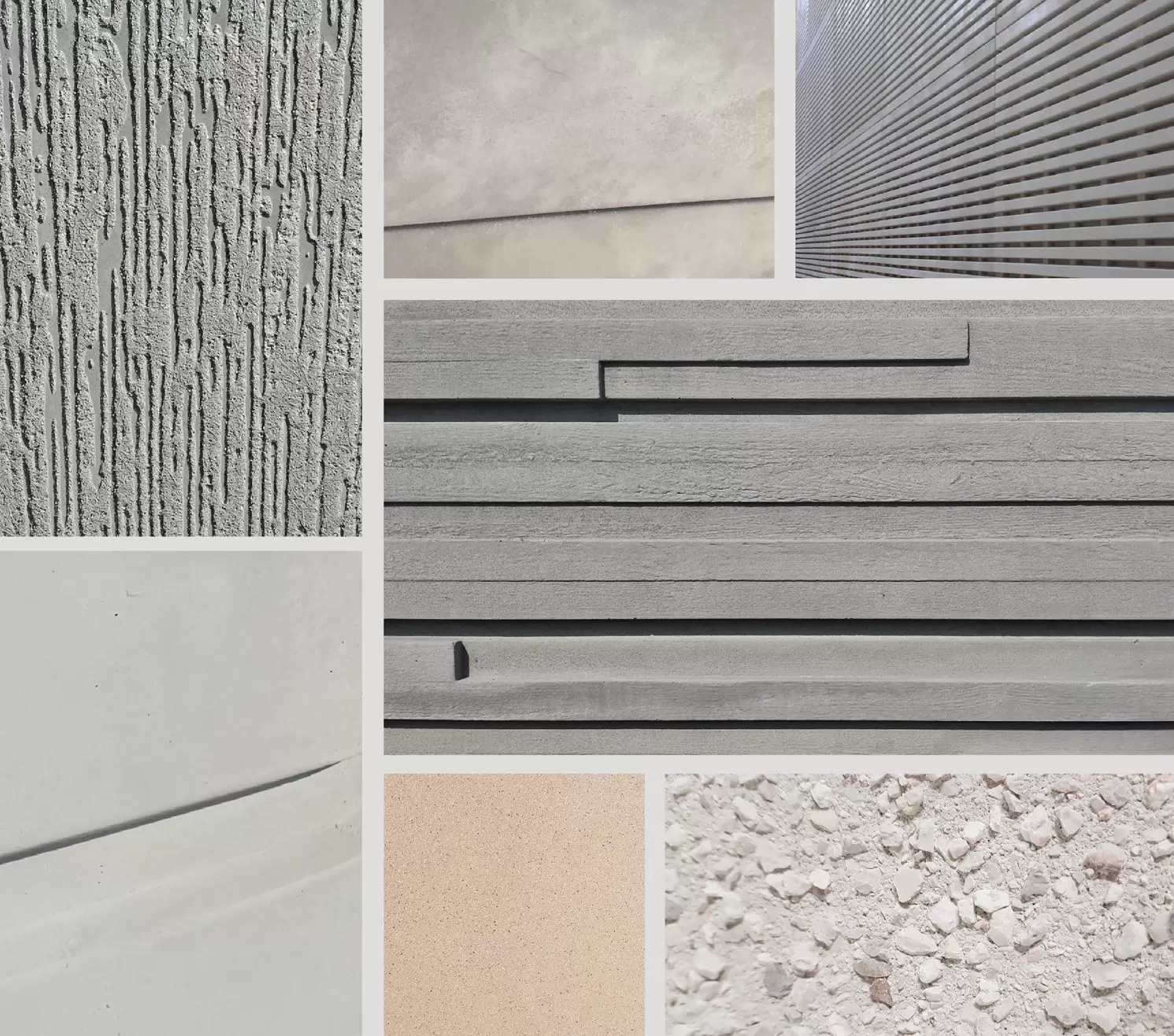
For new projects, we see architects experimenting with different aggregates. Typically, it is an expression of exclusivity, which the architect can achieve by combining and using the different aggregates. And as all elements are coloured through, the combination of these aspects gives endless options for design.
Combining the many surface possibilities with the inherent 3D properties of GRC will give a further boost to the popularity of GRC.
An increasing number of successful projects with a range of different surfaces will most likely foster even more interesting and original projects, where architects can be allowed to dream and unfold their creativity without damaging a project’s budget.
Share on